Coolants are a vital component in CNC machining, serving to optimize performance, extend tool life, and ensure precision. Their primary purpose lies in reducing heat generated by the friction between cutting tools and workpieces, maintaining the dimensional integrity of materials, and preventing tool wear. Effective coolant application directly impacts the efficiency and quality of machining processes.
Understanding the Role of Coolants
In CNC machining, intense heat is produced as tools cut through materials. Without coolant, this heat can distort parts, degrade tool sharpness, and compromise product quality. Coolants not only dissipate this heat but also lubricate the cutting surfaces, reducing friction and enabling smoother operations. This dual function ensures consistent machining accuracy and extends the lifespan of both tools and machines.
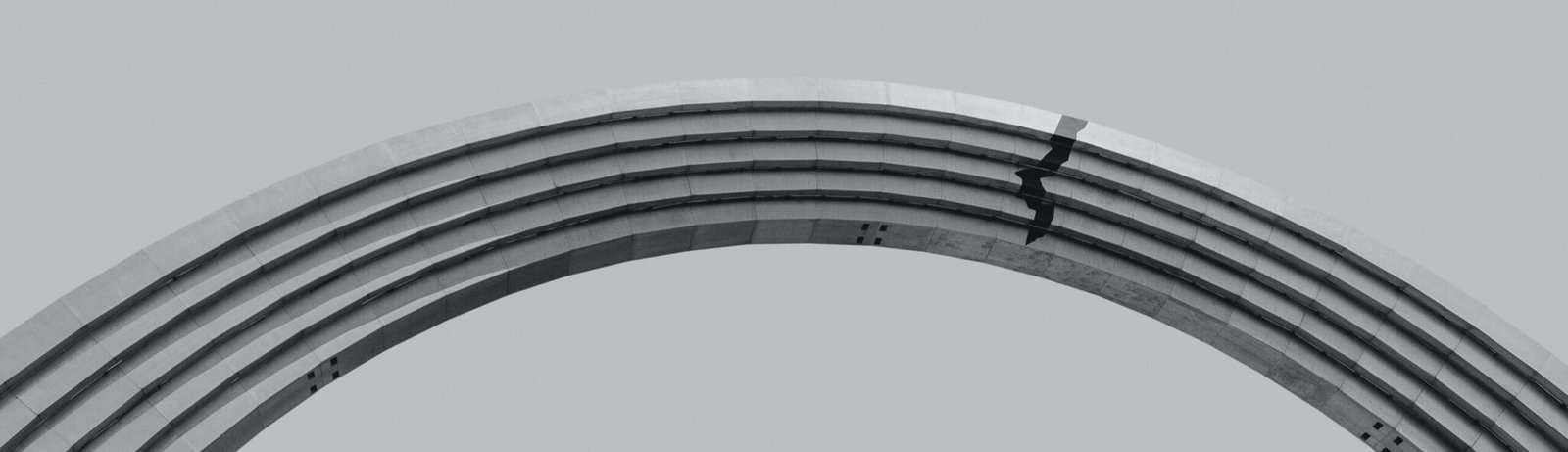
Exploring Coolant Types
CNC machining employs several types of coolants, each suited to specific materials and cutting conditions. Water-soluble coolants, commonly used for their cooling efficiency, are ideal for high-speed operations. On the other hand, oil-based coolants provide superior lubrication, making them suitable for intricate machining tasks or working with tough metals. Synthetic and semi-synthetic coolants offer a balance of cooling and lubrication, meeting diverse operational needs.
“For over 120 years, we have been at the forefront of steel industry innovation. Today, our dedication lies in spearheading the path to a sustainable future for steel and steel manufacturing. Together, we forge a greener and more sustainable tomorrow.”
Effective Coolant Management
Proper management of CNC machine coolant is critical to maximizing its benefits. Regular monitoring and maintenance prevent contamination and maintain the coolant’s effectiveness. Factors like pH balance, concentration levels, and bacterial growth require close attention. Recycling and filtration systems help reduce waste, ensuring environmental compliance and cost efficiency.
Choosing the right coolant influences machining outcomes significantly. It affects surface finish, machining speed, and overall productivity. Moreover, modern advancements in coolant formulations enhance their performance, enabling CNC operations to meet increasingly complex manufacturing demands. Adopting environmentally friendly coolants further aligns machining practices with sustainability goals, reducing ecological footprints while maintaining high-quality output.
CNC machine coolant plays an indispensable role in modern manufacturing, combining heat dissipation, lubrication, and environmental considerations. Understanding its purpose, selecting appropriate types, and managing it effectively are fundamental to achieving optimal machining performance. By integrating innovative coolant solutions and sustainable practices, manufacturers can enhance productivity and meet evolving industry standards with precision and efficiency.
What do you think?
The financing deal is a significant milestone in the project’s progress, and it is a credit to the company’s leadership and team for their tireless efforts in making this vision a reality. The company’s dedication to sustainability and environmental consciousness is a shining example for others in the industry to follow.